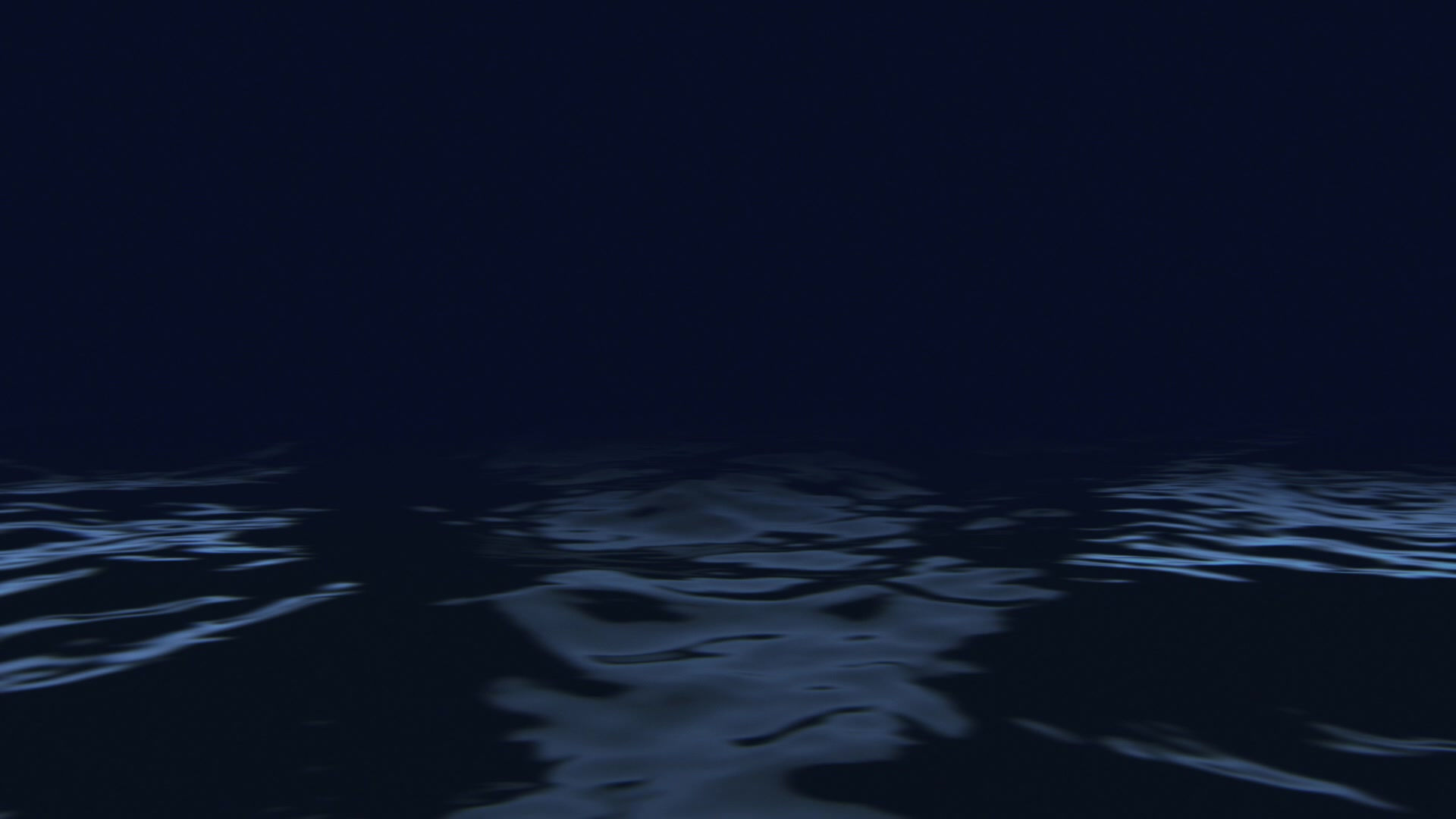
M1171: Principles of Manufacturing and Workshop
1- COURSE DATA
Institution: Benha University - Faculty of Engineering at Benha
Course Code: M1171
Course Name: Principles of Manufacturing and Workshop (A)
Study Plan: Regular System
Department: Mechanical Engineering
Program Name: ---
Specialization: General Mechanical Engineering
Grade: 1st Year
Level: ---
Academic Years: 2018/2019 - 2019/2020 - 2020/2021
Credit Hours: ---
Teaching Hours: Lectures: 2 - Tutorial: 0 - Practical: 3
Duration: 15 Weeks
2- COURSE AIMS
-
This course aims at teaching the students underlying principles of analytical techniques that are commonly used for the evaluation of bulk properties of nanomaterials.
-
These include surface analysis technique FTIR spectroscopy; optical properties evaluation by UV-Vis spectroscopy; crystallographic phase identification by XRD; thermal properties evaluation
-
using TGA and DSC; microstructure investigation by Electron microscopy (SEM and HRTEM); surface area analysis by BET surface area analyzer; magnetic properties by VSM and particle
-
size- surface charge analysis by DLS and seta potential techniques. The course is planned in the form of theoretical and experimental modules for each analysis technique.
3- INTENDED LEARNING OUTCOMES
a. Knowledge & Understanding
-
Basic theories, concepts and specialized knowledge in nanomaterials and their characterization.
-
The effect of modern and advanced nanomaterials and their characterization on the environment.
-
Advanced and developed scientific technologies and theories in nanomaterials and their characterization.
-
Professional ethics and socio-economic impacts of the developed engineering solutions in specific area of nanomaterials and their characterization.
-
Basics and fundamentals of quality issues in nanomaterials and their characterization.
-
Ethics of scientific research and publication.
b. Intellectual Skills
-
Basic theories, concepts and specialized knowledge in nanomaterials and their characterization.
-
The effect of modern and advanced nanomaterials and their characterization on the environment.
-
Advanced and developed scientific technologies and theories in nanomaterials and their characterization.
-
Professional ethics and socio-economic impacts of the developed engineering solutions in specific area of nanomaterials and their characterization.
-
Basics and fundamentals of quality issues in nanomaterials and their characterization.
-
Ethics of scientific research and publication.
c. Professional & Practical Skills
-
Basic theories, concepts and specialized knowledge in nanomaterials and their characterization.
-
The effect of modern and advanced nanomaterials and their characterization on the environment.
-
Advanced and developed scientific technologies and theories in nanomaterials and their characterization.
-
Professional ethics and socio-economic impacts of the developed engineering solutions in specific area of nanomaterials and their characterization.
-
Basics and fundamentals of quality issues in nanomaterials and their characterization.
-
Ethics of scientific research and publication.
d. General & Transferable Skills
-
Basic theories, concepts and specialized knowledge in nanomaterials and their characterization.
-
The effect of modern and advanced nanomaterials and their characterization on the environment.
-
Advanced and developed scientific technologies and theories in nanomaterials and their characterization.
-
Professional ethics and socio-economic impacts of the developed engineering solutions in specific area of nanomaterials and their characterization.
-
Basics and fundamentals of quality issues in nanomaterials and their characterization.
-
Ethics of scientific research and publication.
4- COURSE CONTENTS
CHAPTER 1: Safe Practices
-
Introduction
-
Health and Safety at Work Act (HSWA)
-
Employer’s Responsibilities
-
Safety Policy
-
Employees’ Responsibilities
-
New Regulations for Health and Safety at Work
-
Management of Health and Safety at Work
-
Provision and Use of Work Equipment Regulations (PUWER)
-
Workplace (Health, Safety
and Welfare) Regulations -
Working at Height Regulations (WAHR)
-
Personal Protective Equipment at Work Regulations
-
Health and Safety (Display Screen Equipment) Regulations
-
The Reporting of Injuries, Diseases and Dangerous Occurrences Regulations (RIDDOR)
-
Control of Substances Hazardous to Health (COSHH) Regulations
-
Control of Noise at Work Regulations
-
Control of Vibration at Work Regulations
-
Electrical Hazards
-
The Health and Safety (Safety Signs and Signals) Regulations
-
Safety Signs and Colors
-
Fire
-
Dangerous Substances and Explosive Atmospheres Regulations (DSEAR)
-
First Aid at Work
-
Causes of Accidents
-
General Health and Safety Precautions
CHAPTER 2: Hand Processes
-
Introduction
-
Engineer’s Files
-
The Hacksaw
-
Cold Chisels
-
Scrapers
-
Engineer’s Hammers
-
Screwdrivers
-
Taps
-
Dies
-
Hand Reamer
-
Powered Hand Tools
CHAPTER 3: Marking Out
-
Introduction
-
Datum
-
Co-ordinates
-
Marking Out Equipment
-
Examples of Marking Out
CHAPTER 4: Standards, Measurement & Gauging
-
Introduction
-
Length
-
Angle
-
Dimensional Deviation
-
Gauging
-
Straightness
-
Flatness
-
Squareness
-
Roundness
-
Surface Roughness
CHAPTER 5: Measuring Equipment
-
Introduction
-
Vernier Instruments
-
Micrometers
-
Dial Indicators
-
Modern Measuring Techniques
CHAPTER 6: Cutting Tools & Fluids
-
Introduction
-
Cutting-Tool Materials
-
Cutting Tools
-
Cutting-Tool Maintenance
-
Cutting Speed
-
Cutting Fluids
-
Types of Cutting Fluid
-
Application of Cutting Fluids
-
Safety in the Use of Cutting Fluids
CHAPTER 7: Drilling
-
Introduction
-
The Sensitive Drilling Machine
-
Tool Holding
-
Clamping
-
Cutting Tools on Drilling Machines
-
Drilling Operations
-
Drilling Sheet Metal
-
Drilling Plastics
-
Safety in Use of Drilling Machine
-
Drilling Calculations
CHAPTER 8: Turning (Part 1 + Part 2)
-
Introduction
-
Center-Lathe Elements
-
Center-Lathe Controls
-
Guards
-
Work Holding
-
Center-Lathe Operations
-
Taper Turning
-
Screw-Cutting
-
Safety in Use of Lathe
-
Turning Calculations
CHAPTER 9: Milling (Part 1 + Part 2)
-
Introduction
-
Milling Machine Elements
-
Milling Machine Controls
-
Milling Cutters
-
Cutter Mounting
-
Work Holding
-
The Dividing Head
-
Milling Operations
-
Safety in the Use of Milling Machines
-
Milling Calculations
CHAPTER 10: Surface Grinding
-
Introduction
-
Elements of a Surface Grinding Machine
-
Controls of a Surface Grinding Machine
-
Work Holding
-
Grinding Wheels
-
Surface-Grinding Operations
-
Safety in the Use of Abrasive Wheels
CHAPTER 11: Shapers and Planers
-
Introduction
-
Shaping Machines or Shaper
-
Planing Machines or Planers
CHAPTER 12: Broaching and Bandsawing
-
Broaching
-
Bandsawing
CHAPTER 13: Joining Methods
-
Introduction
-
Mechanical Fasteners
-
Screw Threads
-
Locking Devices
-
Riveting
-
Soft Soldering
-
Solders
-
Brazing
-
Welding
-
Adhesives
-
Electrical Connections
-
Relative Merits of Joining Methods
5- TEACHING AND LEARNING METHODS
6- TEACHING AND LEARNING METHODS FOR DISABLES
7- ACTIVITIES AND SOURCES OF TEACHING AND LEARNING
Assignments are intended to help you master the content, so you should attempt to complete them all. This course employs a variety of assignments, including:
-
Online Readings: provide an introduction to a unit, provide information, or be articles or papers that have been authored by experts in the field.
-
Readings from Books: need to have any required textbooks in advance of starting the course.
-
Exercises: consist of answering questions in a text lecture, writing a paper, or completing some other assignment. Exercises are usually performed offline. You should evaluate your results by comparing them to the results or criteria posted by the Instructor at the end of the lecture notes. Some instructions may include submitting these Exercises to the classroom for your faculty to evaluate.
-
Reviews: are used to help check your understanding of the content. Review results may be included in your final course grade.
-
Reflective Activities: such as writing up a case study, designing a project, or critiquing an assignment may be used as a method for you to analyze, synthesize, and evaluate course content.
-
Collaborative Projects: can involve teams of students working together to participate in study groups, write research papers, make presentations, create case studies, and take part in simulation activities. The projects allow interactions with fellow students and build on facilitation and planning skills.
8- STUDENT ASSESSMENT
a. Student Assessment Methods
b. Assessment Schedule
-
Mid-Term Exam = 7th Week
-
Semi-Final Exam = ---
-
Final Exam = 16th Week
c. Assessment Weights
-
Mid-Term Exam = 15 Marks
-
Lecture Activities = 10 Marks
-
Workshop Activities = 10 Marks
-
Workshop Reports = 10 Marks
-
Attendance = 5 Marks
-
Final Exam = 75 Marks
9- LIST OF REFERENCES AND READING MATERIALS
"Principles of Manufacturing and Workshop (Part A)", A. M. Abdalla, 1st Edition, 2018.
10- MATRIX OF KNOWLEDGE AND SKILLS
11- POLICY
-
Grading Criteria/Timetable: All course activities will be graded within one week of their due date.
-
Extenuating Circumstances: If you have extenuating circumstances that prevent you from completing activities or participating in the class, please contact me to make alternative arrangements. The possibility of alternative arrangements is at the discretion of the instructor. Active communication is the key to overcoming any hurdles you may encounter during the term.
-
Students are expected to be the sole authors of their work. Use of another person's work or ideas must be accompanied by specific citations and references. Though not a comprehensive or exhaustive list, the following are some examples of dishonesty or unethical and unprofessional behavior:
-
Plagiarism: Using another person's words, ideas, or results without giving proper credit to that person; giving the impression that it is the student's own work.
-
Any form of cheating on examinations.
-
Altering academic or clinical records.
-
Falsifying information for any assignments.
-
Submitting an assignment(s) that was partially or wholly completed by another student.
-
Copying work or written text from a student, the Internet, or any document without giving due credit to the source of the information.
-
Submitting an assignment(s) for more than one class without enhancing and refining the assignment, and without first receiving instructor permission. In cases where previous assignments are allowed to be submitted for another class, it is the responsibility of the student to enhance the assignment with additional research and to also submit the original assignment for comparison purposes.
-
Assisting another student with reasonable knowledge that the other student intends to commit any act of academic dishonesty. This offense would include but would not be limited to providing an assignment to another student to submit as his/her own work or allowing another student to copy answers to any test, examination or assignment.
-
Academic dishonesty is a serious offense and may result in the following sanctions:
1st offense: Failure of the assignment in which the action occurred.
2nd offense: Failure of the class in which the action occurred.
3rd offense: Expulsion or permanent dismissal from the University.